Deposition Processes
About
The INL Cleanroom offers a comprehensive set of equipment for thin-film deposition by PVD and CVD techniques.
Description
INL cleanroom has three different physical vapor deposition (PVD) tools: UHV multitarget confocal sputtering tool from Kenosistec, a TIMARIS muti-target module and a TIMARIS flexible target module, both from Singulus Technologies.
The Kenosistec KS1000 PVD cluster tool with a confocal sputter-down configuration, optimized for wafers of up to 200 mm in diameter. The system consists of a flexible UHV multi-target sputtering system with a deposition chamber with 11 magnetrons (2″ diameter) in confocal geometry for co-deposition of materials, and a oxidation chamber. It is especially designed for deposition of conductive and insulating films.
The Multi-Target Module (MTM) PVD cluster tool is especially designed for deposition of ultra-thin films, magnetic films, high-quality metallic, conductive and insulating films and multiple film stack deposition. The system is a UHV single-wafer cluster tool and consists of one transport module, one multi-target PVD module with 10 DC/RF cathodes and one soft etch/oxidation module.
The Flexible Target Module (FTM) PVD cluster tool is especially designed for deposition of high-quality metallic, conductive and insulating films. The system is a UHV single-wafer cluster tool and consists of one transport module, one multi-target PVD module with up to four DC/RF cathodes and one soft etch/oxidation module.
INL cleanroom has two different Chemical Vapour Deposition (CVD) tools: Plasma Enhanced CVD (PECVD) dedicated to silicon oxide and silicon nitride deposition and a CVD hot-wall tube furnace dedicated to graphene and Carbon nanotubes growth.
SPTS MPX CVD Module is dedicated to silicon oxide, silicon nitride and amorphous Silicon deposition by PECVD. It has a single-wafer processing chamber and dual high/low frequency RF options. It uses a plasma to enhance the chemical reaction rates of the precursors, which allows deposition of thin films at lower temperatures (typically <350°C) than in conventional CVD systems. The system is assisted by a multi-sided Transport Module, Vacuum Cassette Elevator(s) configured to accommodate substrates of 200 mm. The vacuum cassette elevator can accommodate substrate cassettes with up to 25 substrates.
CVD FIRST NANO EASY TUBE 3000 tool is a load-locked hot-wall quartz-tube furnace, which is commonly used for deposition of graphene and hexagonal boron nitride 2D materials. The system can operate in APCVD mode (AP=atmospheric pressure) or LPCVD (LP=low-pressure vacuum) modes. It is a 3-zone furnace, with temperature control in a feedback loop that can be operated in Furnace or Cascade modes, for fast heating and precision temperature control, respectively. When in cascade mode, the system oscillates less than 0.2 °C around the set point (up to 1100 °C) for depositions lasting 1 hour or more. Except loading and unloading operations, all the other steps in a complete CVD process are controlled by programmable control software. The system can handle substrates up to 10 cm x 15 cm.
Technical specifications:
— Timaris FTM: Deposition of high-quality metallic, conductive and insulating films.
– Three installed targets: AlSiCu, TiW and Al2O3.
– Deposition of magnetic and non–magnetic layers.
– Substrates up to 200 mm.
– DC/RF Magnetron Sputtering.
– Good uniformity for the deposited films.
– Linear Dynamic Deposition enables the capability to deposit wedge films with a different film thickness across the wafer and to deposit alloy films with adjustable concentration gradients across one wafer.
— Timaris MTM: Deposition of ultra–thin films, magnetic films, high–quality metallic, conductive and insulating films.
– Substrates up to 200 mm.
– Multiple film stack deposition without breaking vacuum.
– DC/RF Magnetron Sputtering.
– Good uniformity of deposited stacks.
– Possibility of hot substrate deposition.
– Collinear Aligning Magnetic Field to align the magnetic easy axis during deposition of ferromagnetic films.
— Kenosistec KS1000: Confocal and co-deposition of a wide range of conductive and non-conductive material.
– DC and RF magnetrons.
– Substrate temperature control up to 350°C.
– Sputter etching in the same chamber as the deposition.
– Possibility to use up to 11 different materials without breaking vacuum.
– Two of the 11 magnetrons also are able to perform reactive sputtering by adding O2 and N2 to the process.
— SPTS PECVD Module: CVD of high/low RF silicon oxide (SiO2), silicon nitride (SiNx), and amorphous silicon (a-Si).
– Single-wafer processing chamber.
– Dual high/low frequency RF options.
– Multi-sided Transport Module, Vacuum Cassette Elevator(s) for substrates of 200 mm.
– Vacuum cassette elevator for substrate cassettes of up to 25 substrates.
– Multiple gases supplied to the process chamber: C4F8, O2, SiH4, H2, N2O, NH3, N2.
— FIRST NANO EASY TUBE 3000: hot-wall quartz-tube furnace for APCVD and LPCVD.
– 3 temperature zones, with operating temperatures up to 1100 °C with an accuracy of +/- 0.2 °C around the setpoint.
– Used for deposition of graphene, hexagonal boron nitride 2D materials and carbon nanotubes.
– Substrates up to 10 cm x 15 cm.
Access Provider / Facilities
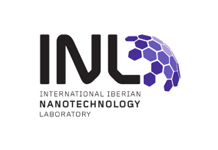