Hot roll mill
About
Mixing hot roll milling machine - it can produce thermoplastic materials master batches up to 0.5 kg range. The material is delivered as irregularly shaped pieces for further processing.
Description
Mixing hot roll milling machine – it can produce thermoplastic materials master batches up to 0.5 kg range. The material is delivered as irregularly shaped pieces for further processing.
Technical specifications:
The roll mill is the simplest batch mixing equipment. A two-roll mill consists of two horizontally placed hollow metal rolls rotating towards each other. The distance between the mill rolls can be varied and this gap is known as nip. The speed difference between the rolls is called friction ratio and it allows the shearing action. The higher friction ratio leads to a higher heat generation in the processed material. The back roll moves faster than the front roll; a common friction ratio is 1:1.25. Two-roll mill mixing is also known as open mill mixing. Friction, speed, and the sizes of the rolls influence the cooling of the material mass and the intensity of its treatment. Depending on the properties of the process material and its desired temperature, the rolls may be internally heated.
The basic mixing operation is illustrated in Fig. The material is charged between the rolls in the form of lumps, pellets, chunks, or powder. As a result of rotation, adhesion, and friction, the material is entrained into the gap between the rolls, and upon discharge it sticks to one of the rolls, depending on their temperature difference and velocities. Another factor is the gap between the rolls. In batch mixing the material after loading passes through the gap between the rolls several times, and the mixing action is due to the different speeds of the rolls. Both the shearing action and entrainment of the material into the gap are very important in the mixing process and transporting of the material through the unit. The gap between the rolls can be adjusted by a massive screw mechanism.
During the operation, cutting of the sheet of the material (“blanket”), folding, and rolling are carried out, which increases the uniformity of the composition. If additives, often in the powder, liquid, or paste form, are to be incorporated, they are added into a rolling “bank” formed between the rolls.
Case study:
An INFRACHIP user might integrate advanced sensors and data processing capabilities into the roll mill to monitor key parameters such as temperature, pressure, and speed more accurately and in real-time. This enhanced monitoring can optimize the mixing process and ensure consistent product quality.
Access Provider / Facilities
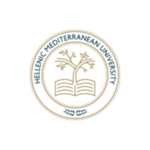